Start Mind Mapping Now!
- Professional Mind Mapping
- Best MS Office Integration
- Build-in Gantt chart & Timeline
- Templates & Tutorials
bbbbbbbbbbb bbbbbb bbb – MindView | Mind Mapping Software
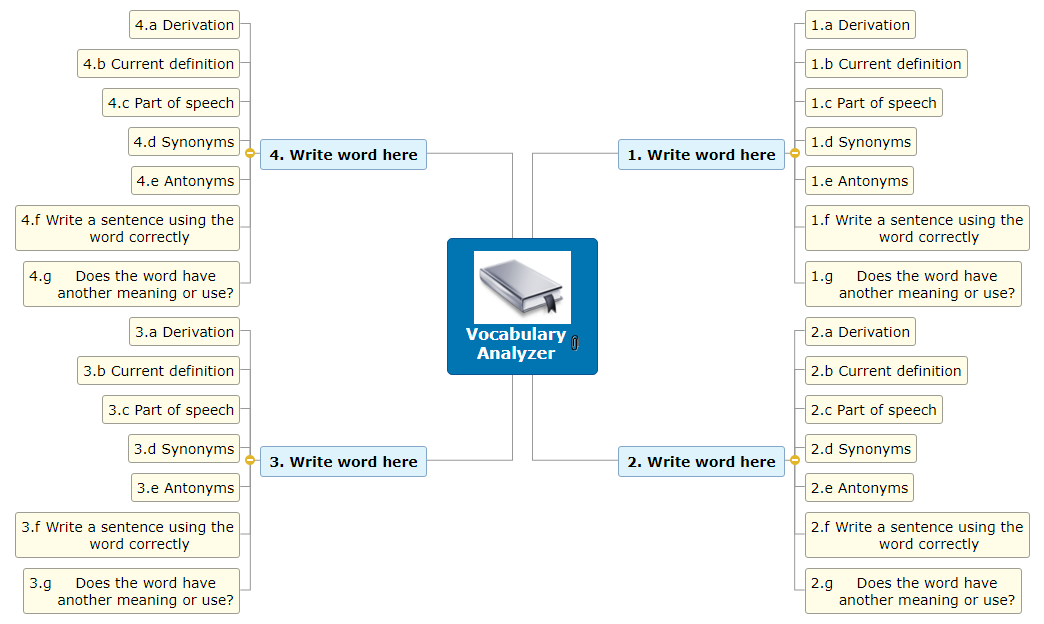
CHAPTER 3. RESEARCH FINDINGS AND ANALYSIS
3.1. TECHNOLOGY
Kristian to et al (2012) stated that for the past decade, technology has had a significant influence on the manufacturing of commodities, and it has an impact on how organizations produce and distribute their products and services. Despite the growth of influence in technology, business leaders around the world continue to struggle with a clear understanding of where and how these technologies can create value, as well as how to successfully focus on the appropriate and timely investment and policies required in the business to unlock that potential value (Das and Nair, 2010).
According to Deutz and Turner (2003) the capacity to deliver on time has become a distinguishing feature of technological transformation and a key to success, and businesses must develop at a rate that allows them to gain a competitive edge, and the technologies they use have an influence on the rate at which they develop. In this new environment, effective, long-term transformation necessitates an immediate and strong emphasis on understanding technologies and how they may add value to the organization, as well as the development of the culture and capabilities needed to execute change (Deutz and Turner, 2003).
The success of the shift is not determined by how effective we commission new technology, but by how well we manage the transition from old skills to new skills, ensuring that the workforce is prepared to run the machinery and evaluate the data it produces (Jiménez, 2009). An increasing body of evidence shows that greater data-driven decision-making, which is facilitated by corporate data analytics solutions, may lead to financial and productivity gains (Jiménez, 2009). The ability of businesses to improve the readiness of their technical teams, skill level of their workforce, procedures, and processes to ensure the inclusive roll-out and adaptation of the technologies, businesses must ensure the availability of underlying infrastructure and focus on data governance and security (Jiménez, 2009).
3.1.1. Inspection devices: The Intellispec vision platform is one of the top inspection systems used in production lines, and it monitors the manufacturing process, rejects faulty goods, and warns end-users to process drift before major issues develop, also saves time and money. According to Berger (2001) the unique Retrospect interface, which visually shows both items and parts, is a key element of the Intellispec program and businesses rely on these devices and software to evaluate product quality.
Figure 2: The Intellispec vision technology
3.2. DATA COLLECTION & INTERPRETATION
3.2.1. Maintenance frequency: This section covers the OEM maintenance recommendation and current plant practices. Table 3 shows the significant component of the camera and recommended maintenance schedule (Pressco, 2013).
Item Description Once per day or shift Once per month
1 Observe Proper inspection Verify that defective parts are being rejected by inserting a known faulty part through inspection X
2 Observe Proper inspection Verify that no stray parts are stuck in or near the inspection module or reject station X
3 Observe Proper inspection Verify that no buildup of dirt or contaminants has occurred on the inspection module, part detector, or conveyor. Clean if necessary. X
4 Observe Proper inspection Verify that each sensor image is appropriately centered, focused, and properly lit. Adjust if necessary. X
5 Vision Processor filter Rinse in clean water; use mild soap and water solution if oily. Cleaning the Vision Processor filter X
6 Cluster Box filters (if applicable) Rinse in clean water; use mild soap and water solution if oily. Cleaning the Cluster Box filters X
7 Part Detect Sensor and Reflector Clean with a soft, clean, oil-free cloth dampened with mild soap and water solution. Wipe dry. Cleaning the Part Detector X
8 Camera lens Clean only with lens tissue and lens cleaner. Be careful not to alter focus or aperture. Cleaning the Camera Lens X
9 Glass surfaces: Beam Splitter and Secondary lens Clean with a soft, clean, oil-free cloth dampened with lens cleaning solution. Cleaning the Chroma pulse Beam Splitter X
Table 3: Intellispec Processor Cabinet, Inspection Modules Chroma pulse and General Components
CHAPTER 4. RECOMMENDATIONS
In this Chapter, the proposals and suggestions are discussed in detail to address the challenges and gaps that were discussed in the research.
4.1 . Review the Asset Care Plans to improve the reliability of the camera
The analysis revealed that the current maintenance procedure is not in compliance with OEM standards. However, the wasted time revealed that with effective asset care plans, almost half of the stoppages can be avoided (maintenance strategies). Secondly, adherence to the current maintenance schedule is insufficient. Finally, the asset management systems in place at the plants differ.
Finally, not all maintenance procedures are stored in the computer system, and some professionals perform maintenance based on their prior expertise rather than a strategy. To address all the discoveries, the team held meetings to evaluate all the maintenance sheets currently on the system for all Voyager-Incan sites in order to identify all the common practices and discrepancies. The session resulted in a recommendation to examine all current Asset Care Plans (ACP) with appropriate Plant representatives and develop a single standard for all Plants.
4.1.1 Proposal
A divisional ACPD (Asset Care Plan Development) procedure is used to examine and assess current maintenance schedules across all plants, as well as review what OEM recommends. Effective asset care plans are produced based on the criticality of the asset, according to the procedure. Based on usefulness, cost, and danger, the camera and light tester are rated criticality "A.". The Optimum Maintenance Mix (OMM) technique is used for criticality "A" assets, followed by Quick Tactic Development (QTD) and Root Case Analyses (RCA) for criticality "B" assets, as indicated in Figure 15.
Figure 15: ACPD Development Process
The OMM procedure is followed by a detailed failure mode analysis, usually down to the component level, of an "A" essential asset or asset system. The result will be a thorough and detailed scheduled maintenance job list that balances multiple maintenance methodologies while concentrating on condition-based maintenance.
4.1.2 Justification
The suggestion is in line with the company's Asset Care Strategy, which aims to ensure that our assets provide maximum availability at the lowest overall life cycle cost. The evaluation also aided in maintaining uniformity across the division. Most maintenance chores were completed, but some operations were not completed or were not recorded on the CMMS to ensure compliance, uniformity, and records. As a result, the decision to hold meetings with all the Plants' representatives helped to verify that the same standards are adhered to and that the CMMS was used to monitor the maintenance schedules.
4.1.3 Financial Analysis
The proposal will require only internal labor from the business expects to execute.
All resources that will be required will be internal:
• Reliability Engineer (x1)
• Maintenance Planners (x4)
• Technicians (x4)
• Electricians (x4)
• Can Makers (x4)
The total time required to execute the process is 8 hours. We can assume that on average the labor will cost R250 per hour.
Therefore, the labor cost will be:
Labor Cost = (Required hours) (Required labor) (hourly cost)
=8 x 17 x 250
= R 34 000
Therefore, the total cost of implementation is R34 000
Benefits:
Assumptions: • Due to overtime, Springs L1 lost a total of 68 hours, while Rosslyn L1 lost a total of 30 hours. Based on the same data, it was determined that at least 5% of the outage could have been avoided. As a result, 5% of 68 plus 30 hours equals 5 hours. This means that if the ACP is implemented, the company should see a 5 hour decrease in downtime per year between the two lines.
• Assume a cost of R2 after overheads are deducted.
• The line moves at a rate of 2400 cans per minute.
Therefore:
The total gain = (Line speed) (Can cost) (available time)
The total gain = (2400) (2) (60x5) =R1 440 000
*Considering that this can be implemented to all sides from one effort, the benefit is higher than the investment. Therefore, this is worth implementing.
4.1.4 Risk Analysis
• Putting ACPD into practice takes time and the necessary resources. It was difficult to find a slot that would accommodate all the participants. As a result, the session was postponed for a month. The first date was set for mid-January, but it wasn't until mid-February that it really happened.
• The specialists' availability within the company.
• The ACPD may necessitate more maintenance time than originally envisaged.
• Tracking the advantages can be challenging because there are other external elements that can alter the camera's effectiveness, such as ageing, increased ambient temperature, and the quality of the downstream cans.
• Plant Management is responsible for ensuring compliance with the plan.
4.1.5 Mitigations
• Consider overtime for the internal resources.
• Consider getting OEM to join the session electronically to assist with expertise.
• Align the planned maintenance with the current Line maintenance.
4.2 Audit Review
• Putting ACPD into practice takes time and the necessary resources. It was difficult to find a slot that would accommodate all the participants. As a result, the session was postponed for a month. The first date was set for mid-January, but it wasn't until mid-February that it really happened.
• The specialists' availability within the company.
• The ACPD may necessitate more maintenance time than originally envisaged.
• Tracking the advantages can be challenging because there are other external elements that can alter the camera's effectiveness, such as ageing, increased ambient temperature, and the quality of the downstream cans.
• Plant Management is responsible for ensuring compliance with the plan and spare changes to these units for optimal performance.
4.2.1 Proposal
With the divisional ACPD (Asset Care Plan Development) plan in place, it is proposed that OEM audits on the inspection units be performed annually via SLA (service level agreement). Based on the audit findings, this will advance the ACPD process plan for effective asset care development and check adherence to the reviewed maintenance plan based on the asset's criticality.
Before handing over to the Plant's technical teams, the initial audit should be completed before the process review is completed (if possible).
The goal of the audit/service visit is to improve system performance by inspecting both the system and the inspection parameters. This would usually include a physical system and software examination, as well as an inspection setup.
4.3.2 Justification
The suggestion is in line with the company's Asset Care Strategy, which aims to ensure that our assets provide maximum availability at the lowest overall life cycle cost.
4.3.3 Proposal
The proposal will require an SLA contract between the OEM and Voyager-Incan to execute.
Chapter 5: IMPLEMENTATION
5.1 Implementation
An Action Learning Program's concept is that the results and recommendations are implemented within the organization to ensure that the recommended solutions are applicable to the problem at hand. Implementations must be in accordance with the suggestions and must address the project's stated problem(s).
5.2 Implementation actions
5.2.1 Execution of the Asset Care Plan
As per the invite presented in Figure 16, meetings were held with plant representatives to examine the plants' maintenance work details and frequency.
Each Plant was required to establish daily, weekly, and monthly camera maintenance plans, according to the OEM's recommendations.
Where:
● Daily check-ups are more concerned with assuring the units' proper operation. The shift electrician is in charge of these inspections.
● The Senior Technician does weekly inspections to confirm that the settings are still in place and that the functionality is working properly.
● Monthly checks are more in-depth inspections and preventative maintenance tasks such as filter cleaning, sensor calibration, and trend analysis.
It was discovered that every plant performs a daily check. The task lists, however, differ between the plants. A daily maintenance check was developed and standardized across all plants, as well as cross-referenced with what the OEMs propose. Second, there was nothing on the system for the weekly checks. However, the team stated that they examine the camera once a week, but there is no evidence to support that claim. As a result, a new weekly plan was designed and installed on the system (CMMS – computerized maintenance management system) to ensure that the Technician was reminded on a weekly basis. Finally, some Plants did not have any Plants for the monthly timetable, while others had distance. The cameras were exposed to dust and heat regardless of whether the production was running, so a mileage-based maintenance method was not a superior frequency. As a result, a monthly (calendar-based) schedule for the Plants was proposed. Figure 17 depicts an example of a monthly schedule work list.
5.2.2 Standard Operating Procedures implementation
When there are problems around the inspection unit, the relevant stakeholders identify and study the causes of the faults and breakdowns; nevertheless, data is lost and cannot be linked to any problem-solving. As a result, data that may be used to improve process quality and, ultimately, product quality is thrown away. To combat data waste, the following steps were taken:
• 5Why reviewing at the MDT meetings
At the Multi-Disciplinary Team (MDT) meetings, one day every week has been set aside to examine the 5Whys. After that, the 5Why documents are preserved for future use.
This effort will assist the company in the following ways:
● When a trigger is reached at the inspection unit area, instils a problem-solving culture in the Plant.
● Improve the quality of 5Why completion and root cause identification.
● Ensure that the appropriate stakeholders are present during problem-solving sessions.
● Make it simple to spot recurring difficulties, which will prompt an RCA to look at all aspects of a problem rather than using the 5Why method.
● Implementation of long-term remedies that address the underlying causes of the issues to prevent recurrence.
● As poorly completed 5Whys are returned to the relevant teams to rewrite, more accountability from the process owners and technical team is required.
Escalation of issues to the Steering Committee
Any concerns relating to the inspection unit that cannot be resolved at the operational and strategic levels are escalated to the Steering Committee, where they are prioritized.
Drive to use basket count information for problem-solving
The inspection unit was designed to blow any non-conforming cans into baskets located at the inspection unit location, as discussed in previous chapters. The Necker operators count the cans in the baskets and record the spoiling as area spoilage on the template provided to them. When a spoiling target is reached, problem-solving is triggered. Basket counts are currently being promoted as a problem-solving tool. The various production teams are constantly engaged in order to urge them to use it.
One of the South African plants has reviewed and improved the Work order (Tactical) document number E-00075 ROS – D1, which was rolled out in September 15, 2020, to ensure that the camera functionality is at its best. These upgrades necessitate shift electricians performing checks twice a day over a twelve-hour shift, which are reviewed and signed by the Electrical Superintendent at the conclusion of each week.
These new enhancements serve as short-interval controls, allowing the inspection unit to function better and avoid problems. It should be emphasized that checks have always been performed, even in the past; nevertheless, there was no consistency, and some external checks were not performed at all. The review has included a thorough SOP, BEVALUINS09, and BEVTEM93 on the new tactical checklist e-00075 ROS – 1D to instruct the Shift Electricians on how to execute the checks step by step, which the Technicians verify if the quality of work done is adequate.
In addition, the new SOP E-11579 ROS – 1W was added to the checklist that the shift electricians use as a safeguard.
This document is completed by day shift technicians once a week, and it has the effect of forcing shift electricians to execute excellent work when performing inspections. The quality management system has evaluated and revised the audit template for the internal and external cameras (Q-Pulse). The audit template has been changed to check for any camera maintenance or setups during the audit period. On March 17, 2021, an audit was undertaken to assess the new template's effectiveness.
The following was recorded during the audit:
● The inspection instructions (BEVALUINS09 and BEVTEM 93) and sections for shift electricians to sign after executing the weekly checks have been included to the work order.
● Shift electricians use the change request template to keep track of any modifications to the production team.
The new implementations are useful to the process, since the Electrical Sup can track whether any shift checks have not been completed and watch any adjustments made at the camera, according to the audit conducted.
More Maps by This User